The Science Behind Bituminous Concrete Design Mix: Composition, Testing, and Performance Implications
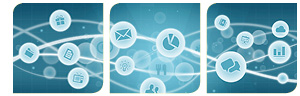
The Foundation of Modern Road Construction
Bituminous concrete is the backbone of modern road infrastructure, providing the flexibility and durability needed for withstanding traffic loads and environmental stressors. But what makes a bituminous mix truly reliable? The answer lies in the careful selection and testing of its components.
The Essentials of Bituminous Mix Design: A Scientific Approach
Bituminous mix design is not just about mixing aggregates and bitumen—it's a carefully engineered process aimed at optimizing performance under real-world conditions. The primary objectives of a well-designed mix include:
✅ Adequate Strength & Stability – Preventing rutting and deformation under heavy loads.
✅ Durability & Resistance to Aging – Ensuring long service life with minimal maintenance.
✅ Fatigue Resistance – Withstanding repeated traffic loads without premature cracking.
✅ Moisture Resistance – Preventing water damage and stripping of bitumen from aggregates.
✅ Workability – Making sure the mix can be easily laid and compacted during construction.
To achieve these properties, the right balance of aggregates, bitumen, and fillers must be maintained.
Breakdown of Key Components and Their Role in Performance
A. Aggregates: The Structural Backbone
Aggregates form 90-95% of the total mix volume, providing the strength and load-bearing capacity. Their properties significantly influence the final performance of the pavement.
🔹 Types of Aggregates Used:
- Coarse Aggregates (Retained on 4.75mm sieve) – Provide strength and load distribution.
- Fine Aggregates (Passing through 4.75mm sieve) – Improve workability and binder adhesion.
🔹 Key Aggregate Properties Affecting Mix Performance:
- Gradation – Determines the void structure, influencing stability and permeability.
- Shape & Texture – Angular aggregates enhance interlocking, improving strength.
- Hardness & Abrasion Resistance – Prevents wear and deformation over time.
- Moisture Susceptibility – Aggregates should not absorb excessive water, which can weaken the mix.
B. Bitumen: The Binding Agent
Bitumen acts as the glue that binds aggregates together while also providing flexibility and water resistance. The properties of bitumen directly impact the durability of the pavement.
🔹 Characteristics of a High-Quality Binder:
- Proper Viscosity & Workability – Ensures good mixing and compaction.
- Elasticity & Cohesion – Enhances resistance to cracking and fatigue.
- Temperature Susceptibility – Bitumen should not soften excessively in hot weather or become brittle in cold climates.
🔹 Types of Bitumen Used in Mix Design:
- Conventional Penetration Grade Bitumen (e.g., 60/70, 80/100) – Used in standard pavements.
- Polymer-Modified Bitumen (PMB) – Improves resistance to rutting and cracking.
- Crumb Rubber Modified Bitumen (CRMB) – Enhances flexibility and recycling potential.
C. Mineral Fillers: Enhancing Mix Stability
Mineral fillers constitute 4-8% of the total mix and are crucial in improving the binding properties of bitumen.
🔹 Commonly Used Fillers:
- Cement
- Lime
- Stone Dust
- Fly Ash
🔹 Functions of Fillers in Mix Design:
- Improve adhesion between bitumen and aggregates.
- Reduce voids in the mix, increasing durability.
- Enhance moisture resistance, preventing stripping.
The Balancing Act: Finding the Perfect Mix Proportion
The ideal bituminous mix must strike a balance between strength, flexibility, and workability. Engineers follow mix design procedures such as:
✔ Marshall Mix Design – Optimizes stability and flow using the Marshall Stability Test.
✔ Superpave Mix Design – Uses performance-graded binders for better durability.
✔ Hveem Mix Design – Measures cohesion and stability for mix optimization.
Each of these approaches helps ensure the mix performs well in real-world conditions, reducing premature failures and maintenance costs.
Why Precision in Mix Design Matters? The Real-World Implications
If bituminous concrete is improperly designed, it can lead to:
Rutting & Deformation – Due to excess bitumen or poor aggregate gradation.
Cracking & Fatigue Failures – Resulting from low binder content or weak aggregates.
Moisture Damage & Stripping – Caused by poor adhesion between bitumen and aggregates.
By following strict testing protocols, highway agencies and construction firms can ensure roads remain durable, cost-effective, and safe.
Conclusion: The Future of Bituminous Mix Design
With advancements in smart materials and sustainable binders, the future of bituminous mix design is evolving rapidly.
The durability and performance of bituminous concrete pavements depend not just on material selection but on rigorous testing at every stage—from mix design to final application. Testing ensures that the mix meets quality, strength, and environmental standards while preventing costly failures.
A well-designed bituminous concrete mix is not just about meeting specifications—it’s about building sustainable and long-lasting roads that can withstand the test of time and traffic.